I dischi abrasivi svolgono un ruolo fondamentale in diversi settori, facilitando la lavorazione e la finitura dei materiali. Tuttavia, come qualsiasi altro utensile, non sono immuni a problemi che possono comprometterne l'efficienza e le prestazioni. In questo articolo, approfondiremo i problemi più comuni dei dischi abrasivi, ne esploreremo le cause profonde e forniremo soluzioni efficaci per un flusso di lavoro fluido.
Introduzione
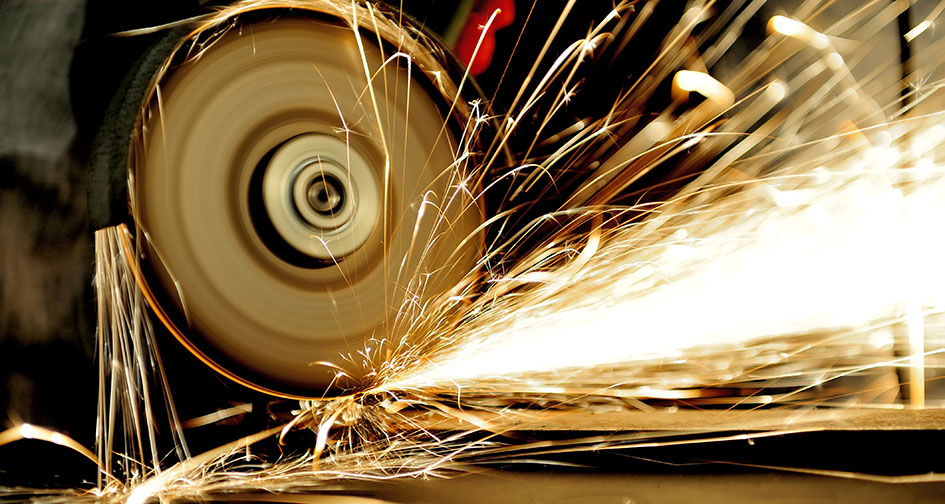
I dischi abrasivi svolgono un ruolo fondamentale in diversi settori, fungendo da strumenti essenziali per i processi di asportazione di materiale, sagomatura e finitura. Comprenderne la definizione, l'importanza in diversi settori e le problematiche comuni è fondamentale per ottimizzarne l'utilizzo e garantire operazioni efficienti.
A. Definizione di dischi abrasivi
I dischi abrasivi sono utensili abrasivi utilizzati nei processi di lavorazione per tagliare, smerigliare o lucidare le superfici dei materiali. Questi dischi sono in genere costituiti da particelle abrasive legate a un materiale di supporto, creando un utensile rotante in grado di rimuovere il materiale in eccesso, levigare le superfici o affilare i bordi. Sono disponibili in varie forme e dimensioni, ciascuna progettata per applicazioni specifiche.
B. Importanza in vari settori
Industria della lavorazione dei metalli:
Nella lavorazione e produzione di metalli, i dischi abrasivi sono essenziali per la sagomatura, la sbavatura e la finitura delle superfici metalliche. Sono comunemente utilizzati con smerigliatrici angolari per ottenere dimensioni precise e una qualità superficiale impeccabile.
Settore edile:
I professionisti dell'edilizia si affidano ai dischi abrasivi per attività quali la preparazione delle superfici in calcestruzzo, la levigatura di bordi irregolari e la rimozione di imperfezioni in materiali come pietra e calcestruzzo.
Industria automobilistica:
I dischi abrasivi sono essenziali nel settore automobilistico per attività che spaziano dall'affilatura di utensili alla sagomatura e finitura di componenti metallici. Contribuiscono alla precisione e alla qualità dei componenti automobilistici.
Industria della lavorazione del legno:
I falegnami utilizzano dischi abrasivi per modellare e levigare le superfici in legno. Questi dischi sono efficaci per rimuovere il materiale in eccesso, rifinire le forme e preparare il legno per ulteriori finiture.
Produzione generale:
I dischi abrasivi trovano applicazione in vari processi di produzione in cui è richiesta un'asportazione precisa del materiale, contribuendo alla produzione di componenti di alta qualità.
C. Problemi comuni affrontati
Usura e abrasione del disco:
L'uso continuo può causare usura e abrasione del disco abrasivo, compromettendone le prestazioni. Ispezioni e sostituzioni regolari sono necessarie per mantenerne l'efficienza.
Surriscaldamento:
Un attrito eccessivo durante l'uso prolungato può causare surriscaldamento, compromettendo la durata del disco e la qualità della finitura superficiale. Sono essenziali misure di raffreddamento adeguate e pause periodiche.
Intasamento:
I dischi abrasivi possono accumulare residui di materiale, riducendone l'efficacia. Una pulizia regolare o la scelta di dischi con caratteristiche anti-intasamento aiutano a prevenire questo problema.
Vibrazioni e oscillazioni:
Squilibri o usura irregolare possono causare vibrazioni o oscillazioni, compromettendo sia la qualità della finitura che la sicurezza del funzionamento. Installazione e bilanciamento corretti sono fondamentali.
Selezione del disco errata:
Scegliere il tipo di disco abrasivo sbagliato per un materiale o un'applicazione specifici può portare a inefficienza e potenziali danni. Una scelta corretta basata sulla compatibilità dei materiali è essenziale.
Comprendere la definizione, l'importanza e le potenziali sfide associate ai dischi abrasivi è essenziale per le aziende che si affidano a questi strumenti. Affrontando le problematiche comuni e garantendone un utilizzo corretto, le aziende possono massimizzare l'efficacia dei dischi abrasivi nelle rispettive applicazioni.
Usura dei dischi abrasivi
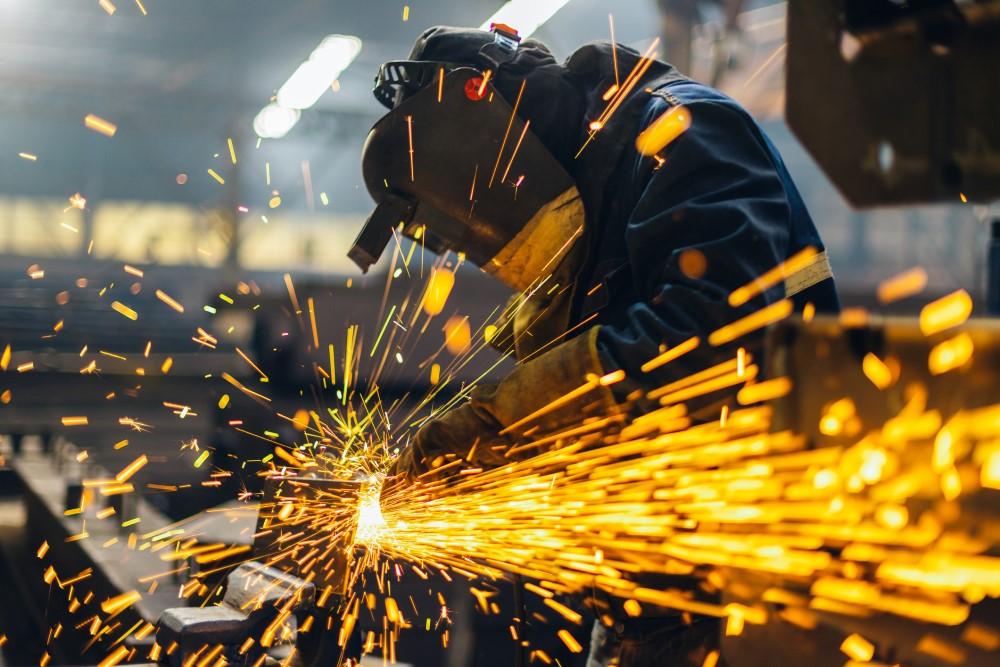
I dischi abrasivi sono utensili essenziali in diversi settori, poiché forniscono l'abrasione necessaria per attività che spaziano dalla lavorazione dei metalli alla lucidatura del calcestruzzo. Comprendere i fattori che contribuiscono all'usura dei dischi abrasivi è fondamentale per ottimizzarne le prestazioni e garantire la sicurezza.
Durezza e composizione del materiale:
Variazione della durezza:I dischi abrasivi lavorano con materiali con diversi livelli di durezza. Materiali abrasivi come metallo e cemento possono presentare durezze significativamente diverse. La continua levigatura su materiali duri accelera l'usura.
Composizione del materiale:La presenza di elementi abrasivi nel materiale da rettificare può influire sull'usura del disco abrasivo. Le particelle abrasive possono accelerare l'usura del disco.
Pressione e forza di macinazione:
Pressione eccessiva:Applicare una pressione eccessiva sul disco abrasivo può accelerarne l'usura. È fondamentale utilizzare la pressione consigliata per l'applicazione specifica per evitare sollecitazioni inutili sul disco.
Forza inadeguata: D'altro canto, una forza insufficiente può causare una macinazione prolungata, generando ulteriore attrito e calore, contribuendo all'usura.
Qualità e composizione del disco:
Qualità del materiale abrasivo:La qualità del materiale abrasivo utilizzato nel disco abrasivo influenza significativamente la sua durata. I materiali abrasivi di alta qualità tendono a resistere all'usura e a mantenere l'affilatura più a lungo.
Agente legante:Il legante che tiene insieme le particelle abrasive gioca un ruolo cruciale. Un legante ben progettato aumenta la durata del disco.
Condizioni dell'ambiente di lavoro:
Temperatura:Le elevate temperature generate durante la rettifica possono influire sulla composizione del disco. Il calore eccessivo indebolisce l'agente legante e ne accelera l'usura.
Umidità e contaminanti:L'esposizione all'umidità o a contaminanti nell'ambiente di lavoro può compromettere l'integrità del disco abrasivo, provocandone un'usura più rapida.
Tecnica dell'operatore:
Tecnica corretta:L'abilità e la tecnica dell'operatore sono fondamentali. Un uso improprio, come la molatura con angolazioni non corrette o l'applicazione di una forza eccessiva, può contribuire a un'usura irregolare e ridurre la durata del disco.
Ispezioni regolari:Gli operatori devono ispezionare regolarmente il disco abrasivo per individuare eventuali segni di danneggiamento o usura. I dischi che mostrano un'usura superiore a un certo punto devono essere sostituiti tempestivamente.
Compatibilità dimensioni disco e giri/min:
Dimensioni corrette:Utilizzare dischi della dimensione corretta per la smerigliatrice è fondamentale. Dischi di dimensioni non corrette possono usurarsi in modo non uniforme o rappresentare rischi per la sicurezza.
Compatibilità RPM:Il rispetto del numero di giri al minuto (RPM) consigliato per il disco abrasivo garantisce prestazioni ottimali e previene l'usura prematura.
La manutenzione regolare, il rispetto delle condizioni operative raccomandate e la scelta del disco abrasivo più adatto sono pratiche essenziali per ridurre al minimo l'usura. Comprendendo i fattori che influenzano l'usura, gli operatori possono migliorare la longevità e l'efficienza dei dischi abrasivi, contribuendo a operazioni di rettifica più sicure e produttive.
Rettifica irregolare
La rettifica non uniforme si riferisce alla situazione in cui la superficie da rettificare non raggiunge una finitura uniforme e liscia. Questo problema può verificarsi per vari motivi e può influire sulla qualità del pezzo in lavorazione. Ecco i fattori comuni che contribuiscono alla rettifica non uniforme e le possibili soluzioni:
Selezione errata della mola abrasiva:
Soluzione:Assicuratevi che la mola abrasiva sia adatta al materiale da lavorare. Materiali diversi richiedono proprietà abrasive specifiche. Scegliete il tipo di mola, la grana e il legante più adatti all'applicazione.
Ravvivatura impropria della mola:
Causa:Una mola abrasiva non adeguatamente rettificata può causare un'usura non uniforme e un taglio inefficace.
Soluzione:Ravvivare regolarmente la mola abrasiva per mantenerne la forma e rimuovere eventuali detriti accumulati. Una ravvivatura corretta garantisce una superficie di taglio uniforme.
Fluido di rettifica o refrigerante inadeguato:
Causa:L'uso insufficiente o improprio del fluido di rettifica può causare un aumento dell'attrito e del calore, con conseguente rettifica non uniforme.
Soluzione:Utilizzare un fluido di rettifica o un refrigerante appropriato per dissipare il calore e ridurre l'attrito. Un raffreddamento adeguato è essenziale per ottenere risultati uniformi.
Parametri di macinazione errati:
Causa:L'utilizzo di parametri di rettifica errati, quali velocità, velocità di avanzamento o profondità di taglio eccessive, può dare luogo a una rettifica non uniforme.
Soluzione:Regolare i parametri di macinazione in base al materiale e ai requisiti dell'applicazione. Fare riferimento alle raccomandazioni del produttore per le impostazioni ottimali.
Mola usurata:
Causa:Una mola usurata potrebbe non garantire una superficie di taglio uniforme, con conseguente rettifica non uniforme.
Soluzione:Sostituire la mola abrasiva al termine della sua vita utile. Ispezionarla regolarmente per individuare eventuali segni di usura.
Pressione o velocità di alimentazione non uniformi:
Causa:Una pressione non uniforme o velocità di avanzamento non costanti durante la rettifica possono causare una rimozione irregolare del materiale.
Soluzione:Applicare una pressione uniforme e mantenere una velocità di avanzamento costante su tutto il pezzo. L'abilità dell'operatore e l'attenzione ai dettagli sono fondamentali.
Problemi della macchina:
Causa:Problemi meccanici della rettificatrice, come disallineamenti o problemi con il mandrino, possono dare luogo a una rettifica non uniforme.
Soluzione:Eseguire controlli di manutenzione periodici sulla rettificatrice. Risolvere tempestivamente eventuali problemi meccanici per garantirne il corretto funzionamento.
Fissaggio del pezzo:
Causa:Pezzi fissati male o disallineati possono dare luogo a una rettifica non uniforme.
Soluzione:Assicurare il corretto fissaggio e allineamento del pezzo in lavorazione. Fissarlo saldamente per evitare movimenti durante il processo di rettifica.
Per affrontare una rettifica non uniforme è necessario combinare una corretta configurazione delle attrezzature, parametri operativi corretti e pratiche di manutenzione regolari. Gli operatori devono essere formati per identificare e correggere tempestivamente i problemi, al fine di ottenere risultati di alta qualità e costanti nelle applicazioni di rettifica. Ispezioni regolari e il rispetto delle migliori pratiche contribuiscono a una rimozione efficiente e uniforme del materiale durante il processo di rettifica.
Problemi di surriscaldamento
Il surriscaldamento durante la rettifica è un problema comune che può influire sulle prestazioni sia della mola che del pezzo in lavorazione. Il calore eccessivo può causare diversi problemi, tra cui una riduzione della durata della mola, danni termici al pezzo e una riduzione complessiva dell'efficienza di rettifica. Ecco possibili cause e soluzioni per affrontare i problemi di surriscaldamento:
Parametri di macinazione errati:
Causa:L'utilizzo di parametri di rettifica non corretti, come velocità, velocità di avanzamento o profondità di taglio eccessive, può generare calore eccessivo.
Soluzione:Regolare i parametri di macinazione entro l'intervallo consigliato. Consultare le istruzioni del produttore per le impostazioni ottimali in base al materiale da macinare.
Raffreddamento o lubrificazione inadeguati:
Causa:L'uso insufficiente di refrigerante o fluido di rettifica può causare un aumento dell'attrito e del calore.
Soluzione:Assicurare un adeguato apporto di refrigerante o lubrificante durante il processo di rettifica. Un raffreddamento adeguato aiuta a dissipare il calore e previene danni termici.
Selezione ruota errata:
Causa:La scelta di una mola abrasiva con specifiche non idonee per il materiale da rettificare può causare il surriscaldamento.
Soluzione:Selezionare una mola abrasiva con il tipo di abrasivo, la grana e il legante corretti per l'applicazione specifica. L'abbinamento della mola al materiale riduce al minimo la generazione di calore.
Problemi relativi al materiale del pezzo:
Causa:Alcuni materiali, in particolare quelli con scarsa conduttività termica, sono più soggetti al surriscaldamento durante la macinazione.
Soluzione:Adattare i parametri di rettifica ai materiali con minore conduttività termica. Valutare l'utilizzo di una mola specifica per materiali sensibili al calore.
Problemi di ravvivatura delle mole:
Causa:Eventuali irregolarità o una ravvivatura non idonea della mola abrasiva possono causare un contatto non uniforme e un accumulo di calore.
Soluzione:Ravvivare regolarmente la mola abrasiva per mantenerne la forma e rimuovere eventuali vetri o detriti accumulati. Le mole adeguatamente ravvivate garantiscono prestazioni di rettifica costanti.
Manutenzione inadeguata della macchina:
Causa:Le rettificatrici sottoposte a scarsa manutenzione possono contribuire a problemi di surriscaldamento.
Soluzione:Eseguire la manutenzione regolare della rettificatrice, incluso il controllo degli impianti di raffreddamento, l'ispezione delle attrezzature di ravvivatura delle mole e la verifica del corretto allineamento. Risolvere tempestivamente eventuali problemi meccanici.
Flusso di refrigerante delle ruote insufficiente:
Causa:Un flusso inadeguato del refrigerante nella zona di rettifica può comportare una ridotta dissipazione del calore.
Soluzione:Controllare e ottimizzare il sistema di erogazione del refrigerante. Assicurarsi che il refrigerante raggiunga efficacemente la zona di rettifica per mantenere l'efficienza di raffreddamento.
Tempo di macinazione eccessivo:
Causa:Le sessioni di macinazione prolungate senza pause possono contribuire all'accumulo di calore.
Soluzione:Eseguire la rettifica a intermittenza e prevedere pause per evitare un eccessivo accumulo di calore. Questo approccio è particolarmente importante per lavori di rettifica di grandi dimensioni o impegnativi.
Affrontare i problemi di surriscaldamento durante la rettifica richiede un approccio completo che includa una corretta configurazione delle attrezzature, parametri di rettifica adeguati e procedure di manutenzione regolari. Gli operatori devono monitorare e controllare la generazione di calore durante il processo di rettifica per garantire prestazioni ottimali, una maggiore durata dell'utensile e risultati di alta qualità.
Problemi di vibrazioni
Vibrazioni eccessive durante le operazioni di rettifica possono causare diversi problemi, tra cui una riduzione della qualità superficiale, una maggiore usura degli utensili e potenziali danni alla rettificatrice. Affrontare i problemi di vibrazione è fondamentale per ottenere processi di rettifica precisi ed efficienti. Ecco possibili cause e soluzioni per mitigare i problemi di vibrazione:
Usura irregolare delle ruote:
Causa:L'usura irregolare della mola abrasiva può causare un contatto non uniforme con il pezzo in lavorazione, provocando vibrazioni.
Soluzione:Ispezionare e ravvivare regolarmente la mola abrasiva per mantenere una superficie uniforme e piana. Una corretta manutenzione della mola aiuta a ridurre al minimo le vibrazioni.
Mola sbilanciata:
Causa:Uno squilibrio nella mola, dovuto a un'usura irregolare o a difetti di fabbricazione, può causare vibrazioni.
Soluzione:Bilanciare la mola utilizzando un'equilibratrice. L'equilibratura garantisce una distribuzione uniforme del peso e riduce le vibrazioni durante il funzionamento.
Calibrazione inadeguata della macchina:
Causa:Una calibrazione scadente o un disallineamento dei componenti della macchina, come il mandrino della ruota o il tavolo di lavoro, possono contribuire alle vibrazioni.
Soluzione:Calibrare e allineare regolarmente i componenti della macchina per garantirne il corretto funzionamento. Seguire le istruzioni del produttore per la configurazione e l'allineamento della macchina.
Squilibrio del pezzo:
Causa:Un pezzo in lavorazione non uniforme o fissato in modo non corretto può creare squilibrio e indurre vibrazioni.
Soluzione:Fissare correttamente il pezzo in lavorazione, assicurandosi che sia posizionato e bloccato in modo uniforme. Risolvere eventuali problemi di squilibrio prima di iniziare il processo di rettifica.
Selezione ruota errata:
Causa:L'utilizzo di una mola abrasiva con specifiche non idonee può provocare vibrazioni.
Soluzione:Selezionare una mola abrasiva con il tipo di abrasivo, la grana e il legante corretti per il materiale da rettificare. L'abbinamento della mola all'applicazione riduce al minimo le vibrazioni.
Usura della macchina:
Causa:Componenti della macchina usurati o danneggiati, come cuscinetti o mandrini, possono contribuire alle vibrazioni.
Soluzione:Ispezionare e sostituire regolarmente le parti usurate della macchina. Una corretta manutenzione aiuta a prevenire vibrazioni eccessive e a prolungare la durata della rettificatrice.
Flusso di refrigerante inadeguato:
Causa:Un flusso di refrigerante insufficiente nella zona di rettifica può causare accumulo di calore e vibrazioni.
Soluzione:Ottimizzare il sistema di erogazione del refrigerante per garantire un raffreddamento adeguato. Un raffreddamento efficace riduce il rischio di dilatazione e contrazione termica, che possono causare vibrazioni.
Problemi con il portautensili:
Causa:Problemi con il portautensili o con l'interfaccia del mandrino possono causare vibrazioni.
Soluzione:Assicurarsi che il portautensili sia montato saldamente e correttamente allineato con il mandrino. Utilizzare portautensili di alta qualità e sottoposti a manutenzione adeguata per ridurre al minimo le vibrazioni.
Fondazione della macchina:
Causa:Una base di appoggio scadente o un supporto inadeguato della macchina possono amplificare le vibrazioni.
Soluzione:Assicurarsi che la rettificatrice sia installata su una base stabile e progettata correttamente. Risolvere eventuali problemi strutturali per ridurre al minimo le vibrazioni trasmesse alla macchina.
Per affrontare efficacemente i problemi di vibrazione nella rettifica, è necessario combinare un'adeguata manutenzione della macchina, la scelta della mola e la movimentazione del pezzo. Gli operatori devono implementare procedure di ispezione e manutenzione regolari per identificare e risolvere tempestivamente i problemi, migliorando così le prestazioni e la qualità della rettifica.
Problemi di caricamento durante la macinazione
Il carico durante la rettifica si riferisce al fenomeno per cui gli spazi tra i grani abrasivi sulla mola si riempiono di materiale da rettificare, con conseguente riduzione dell'azione di taglio e aumento dell'attrito. Il carico può influire negativamente sull'efficienza e sulla qualità del processo di rettifica. Ecco possibili cause e soluzioni per risolvere i problemi di carico:
Materiale morbido del pezzo:
Causa:La macinazione di materiali morbidi può causare il rapido intasamento dei grani abrasivi.
Soluzione:Utilizzare una mola abrasiva con grana più grossa e struttura aperta quando si lavora su materiali più morbidi. Questo aiuta a prevenire il caricamento rapido e consente un'efficiente rimozione dei trucioli.
Contaminazione dei materiali:
Causa:I contaminanti presenti nel materiale del pezzo in lavorazione, come oli, grasso o residui di refrigerante, possono contribuire al carico.
Soluzione:Assicurarsi che il pezzo in lavorazione sia adeguatamente pulito prima della rettifica per rimuovere eventuali contaminanti. Utilizzare fluidi da taglio o refrigeranti appropriati per ridurre al minimo il carico.
Applicazione errata del refrigerante:
Causa:Un'applicazione inadeguata o impropria del refrigerante può portare a una lubrificazione e a un raffreddamento insufficienti, con conseguente sovraccarico.
Soluzione:Ottimizzare il flusso e la concentrazione del refrigerante. Assicurarsi che il refrigerante raggiunga efficacemente la zona di rettifica per lubrificare e raffreddare il processo, prevenendo il sovraccarico.
Affilatura della ruota insufficiente:
Causa:Le mole abrasive usurate o smussate sono più soggette a intasamento perché perdono la loro efficienza di taglio.
Soluzione:Affilare e ravvivare regolarmente la mola per mantenerne l'affilatura. Utilizzare un ravvivatore per esporre nuovi grani abrasivi e migliorare l'azione di taglio.
Bassa velocità delle ruote:
Causa:Se si aziona la mola a bassa velocità, la forza centrifuga potrebbe non essere sufficiente per espellere i trucioli, con conseguente inceppamento.
Soluzione:Assicurarsi che la rettificatrice funzioni alla velocità consigliata per la specifica combinazione mola-pezzo. Velocità più elevate possono contribuire a una migliore rimozione dei trucioli.
Pressione eccessiva:
Causa:Applicando una pressione eccessiva durante la rettifica, il materiale può entrare nella mola, causando un inceppamento.
Soluzione:Utilizzare una pressione di molatura moderata e costante. Regolare la velocità di avanzamento per consentire alla mola di tagliare in modo efficiente, senza una pressione eccessiva che potrebbe causare inceppamenti.
Specifiche delle ruote errate:
Causa:L'utilizzo di una mola con specifiche errate per il materiale da rettificare può causare inceppamenti.
Soluzione:Selezionare una mola abrasiva con il tipo di abrasivo, la grana e il legante appropriati per l'applicazione specifica. Scegliere la mola adatta al materiale aiuta a prevenire l'intasamento.
Pulizia inadeguata del liquido di raffreddamento:
Causa:Un refrigerante contaminato o vecchio può contribuire a creare problemi di caricamento.
Soluzione:Pulire e sostituire regolarmente il liquido di raffreddamento per prevenire l'accumulo di contaminanti. Un liquido di raffreddamento fresco e pulito migliora la lubrificazione e il raffreddamento, riducendo la probabilità di sovraccarichi.
Tecnica di medicazione non corretta:
Causa:Una ravvivatura non corretta della mola abrasiva può causare irregolarità e carichi.
Soluzione:Ravvivare correttamente la mola utilizzando l'apposito utensile. Assicurarsi che il profilo della mola sia uniforme e privo di irregolarità per evitare sovraccarichi.
Per affrontare efficacemente i problemi di carico, è fondamentale combinare la corretta selezione della mola, la corretta configurazione della macchina e le corrette pratiche di manutenzione. Gli operatori devono seguire le procedure raccomandate, utilizzare parametri di rettifica adeguati e ravvivare regolarmente la mola per ridurre al minimo il carico e ottimizzare le prestazioni di rettifica.
La scelta del disco abrasivo giusto è fondamentale per ottenere risultati ottimali in diverse applicazioni di lavorazione dei metalli e fabbricazione. La scelta dipende da fattori quali il materiale da lavorare, la finitura desiderata e il tipo di smerigliatrice utilizzata.
Scegliere il disco abrasivo giusto
Compatibilità dei materiali:
Metalli ferrosi (acciaio, ferro):Utilizzare dischi da sbavo specificamente progettati per metalli ferrosi. Questi dischi contengono spesso abrasivi adatti alla durezza dell'acciaio e sono meno soggetti a incrostazioni.
Metalli non ferrosi (alluminio, ottone):Scegliete dischi con abrasivi adatti ai metalli più teneri per evitare intasamenti. I dischi in ossido di alluminio o carburo di silicio sono le scelte più comuni.
Materiale abrasivo:
Ossido di alluminio:Adatto per la molatura generica di metalli ferrosi. Resistente e versatile.
Zirconia Allumina:Offre maggiore efficienza di taglio e durata, rendendolo adatto alla molatura aggressiva di metalli ferrosi e non ferrosi.
Carburo di silicio:Ideale per la molatura di metalli non ferrosi e pietre. È più affilato ma meno resistente dell'ossido di alluminio.
Grana:
Grana grossa (24-36):Rapida asportazione del materiale e rettifica pesante.
Grana media (40-60):Bilancia l'asportazione di materiale e la finitura superficiale.
Grana fine (80-120):Fornisce una finitura liscia, adatta alla preparazione delle superfici e alla levigatura leggera.
Tipo di ruota:
Tipo 27 (Centro depresso):Disco abrasivo standard con superficie piana, ideale per la levigatura di superfici e la lavorazione dei bordi.
Tipo 29 (conico):Design angolato per una rimozione aggressiva del materiale e una migliore miscelazione della superficie.
Tipo 1 (dritto):Utilizzato per applicazioni di taglio. Fornisce un profilo sottile per un taglio preciso.
Applicazione:
Macinazione:Dischi abrasivi standard per la rimozione e la sagomatura di materiali.
Taglio:Utilizzare dischi da taglio per tagliare il metallo, ottenendo un bordo dritto e pulito.
Dischi lamellari:Combina levigatura e finitura in un unico strumento. Adatto per la finitura e la levigatura delle superfici.
Compatibilità con Grinder:
Assicurarsi che il disco abrasivo sia compatibile con il tipo e la velocità della smerigliatrice utilizzata. Verificare le raccomandazioni del produttore per il numero massimo di giri al minuto (RPM) del disco.
Specificità del compito:
Rimozione pesante di materiale:Per una rimozione efficiente del materiale, scegliere una grana grossa e un disco di tipo 27 o 29.
Finitura superficiale:Per finiture più lisce, optare per grane da medie a fini con dischi lamellari.
Considerazioni sulla sicurezza:
Seguire le linee guida di sicurezza, tra cui indossare adeguati dispositivi di protezione individuale (DPI), come occhiali e guanti.
Scegli dischi rinforzati per maggiore durata e sicurezza.
Marchio e qualità:
Scegli dischi di marchi affidabili, noti per qualità e costanza. I dischi di alta qualità offrono prestazioni e durata migliori.
Considerazioni sui costi:
Bilanciate il costo iniziale con la durata prevista e le prestazioni del disco abrasivo. I dischi di alta qualità possono avere un costo iniziale più elevato, ma possono offrire un valore maggiore nel tempo.
Considerando questi fattori, gli operatori possono scegliere il disco abrasivo più adatto alle loro specifiche applicazioni, garantendo efficienza, sicurezza e risultati ottimali.
Conclusione
In conclusione, la scelta del disco abrasivo appropriato è un aspetto fondamentale per ottenere risultati di successo nella lavorazione e fabbricazione dei metalli. La scelta dipende da diversi fattori, come il materiale da lavorare, la finitura desiderata e il tipo di smerigliatrice utilizzata. Considerando la compatibilità del materiale, il tipo di abrasivo, la granulometria, il tipo di mola, l'applicazione, la compatibilità della smerigliatrice, la specificità del compito, la sicurezza, la qualità del marchio e il costo, gli operatori possono prendere decisioni consapevoli per migliorare l'efficienza e la sicurezza nei loro processi di rettifica.
È fondamentale rispettare le linee guida di sicurezza, indossare adeguati dispositivi di protezione individuale e seguire le raccomandazioni del produttore per la compatibilità tra smerigliatrice e disco. Che si tratti di asportazione pesante, finitura superficiale o applicazioni di taglio, il disco da smerigliatura giusto può influire significativamente sulla qualità e l'efficienza del lavoro.
Inoltre, controlli periodici per verificare l'usura, affrontare problemi quali surriscaldamento e vibrazioni e comprendere i problemi di carico contribuiscono a prolungare la durata del disco abrasivo e a garantire prestazioni costanti.
In sintesi, un approccio sistematico e ben informato alla selezione, all'uso e alla manutenzione dei dischi abrasivi è fondamentale per ottenere risultati ottimali, aumentare la produttività e garantire un ambiente di lavoro sicuro.
Data di pubblicazione: 12 gennaio 2024